One of the keys to achieving the "double carbon" goal is the transportation industry. On the one hand, the transportation industry is the main field of global greenhouse gas emissions. Moreover, with the continuous improvement of China's automobile ownership, the carbon emission of the automobile industry will become the focus of the "double carbon" goal.
On the other hand, there is still a certain gap between China's car ownership per thousand people and developed countries. With the economic recovery and gradual improvement of urbanization after the epidemic, the development of new energy vehicles will help to achieve "double carbon". From the working principle of new energy vehicles, it can be seen that the carbon emission reduction effect of new energy vehicles is obvious compared with traditional fuel vehicles.
The development of new energy vehicles is ushering in new opportunities under the background of "double carbon".
Thermal management of power battery
As the power source of new energy vehicles, power battery is undoubtedly the core of the core.
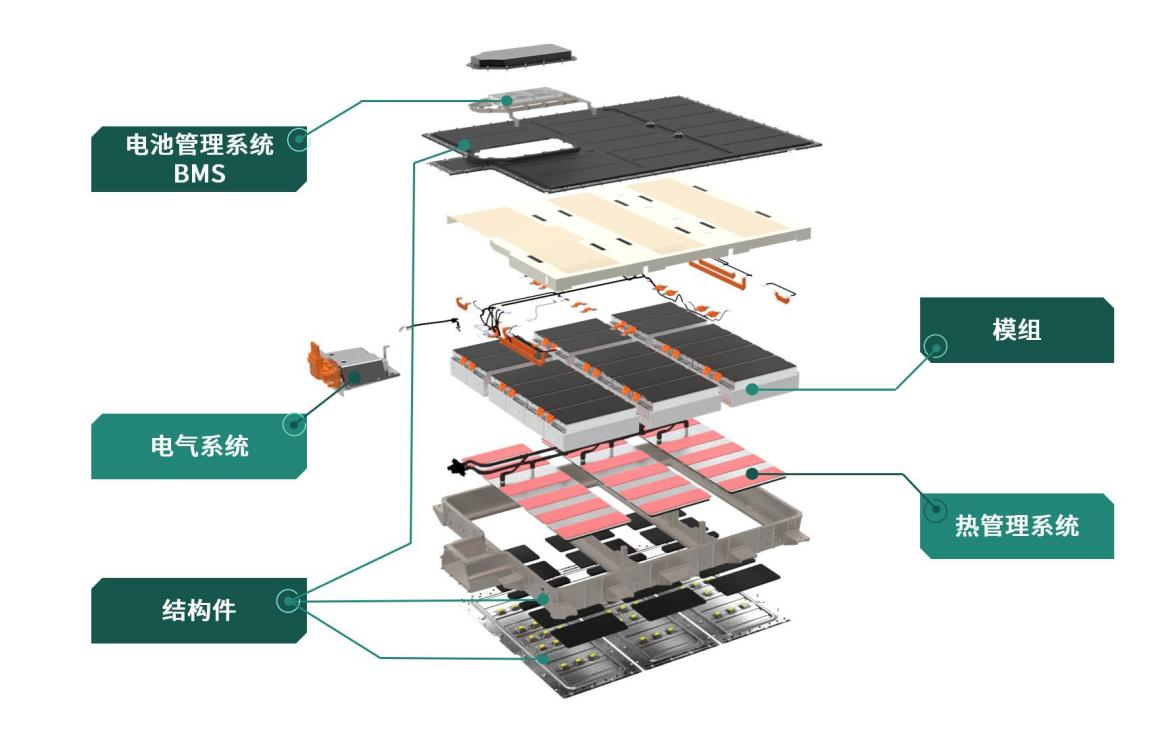
Power battery components mainly rely on the conversion of chemical energy into electric energy to provide power source for electric vehicles. At low temperature, the thickening of electrolyte leads to the obstruction of the movement of conductive medium and the reduction of electrochemical reaction rate and reaction depth, which leads to the decline of battery capacity. The macro of power battery shows the phenomenon of "power loss" of electric vehicle in winter environment. On the other hand, too high temperature will cause a series of side reactions in the battery, which will not only affect the service life of the battery, but also have potential safety hazards. Because of the important influence of temperature on electrochemical reaction, the restriction of power battery by temperature is also very obvious.
The space of the vehicle chassis is limited, and the battery modules must be closely arranged. However, on the one hand, closely arranged batteries are easy to lead to heat accumulation, on the other hand, the temperature of cells in different positions is often not exactly the same. Therefore, using a reasonable thermal management mode to regulate the battery working temperature and maintain the consistency of cell temperature in the battery pack is of great significance for the life and safety of the battery pack. Especially in the industry trend of pursuing high endurance and fast charging, excellent power battery thermal management system determines the service life and safety of electric vehicles.
Application of polyurethane thermal conductive structural adhesive
According to the cooling medium, the thermal management system can be divided into air cooling, liquid cooling, phase change cooling, heat pipe cooling, etc. At present, the power battery industry occupies the "C" position, which belongs to the liquid cooling mode. In the liquid cooling mode, the thermal conductive adhesive plays an important auxiliary role. In order to test the thermal conductivity of thermal conductive adhesive, a famous scientific research institution established a single cell heating model, simulated and analyzed the heating of battery module under different discharge rates, and studied and compared the balanced heat dissipation effect of thermal conductive adhesive with different thermal conductivity on lithium battery.
The results show that the higher the thermal conductivity, the more obvious the thermal conductive adhesive is to reduce the temperature rise and temperature difference of the battery, and the more balanced the temperature distribution of the battery. Because the optimal working temperature band of power battery cell is very narrow, generally between 20-40 ℃, the heat conduction of thermal conductive adhesive can effectively reduce the temperature of cell and the temperature difference between cells, which has a very significant effect on maintaining the normal operation of battery thermal management system.
(balanced heat dissipation effect of thermal conductive adhesive on battery)
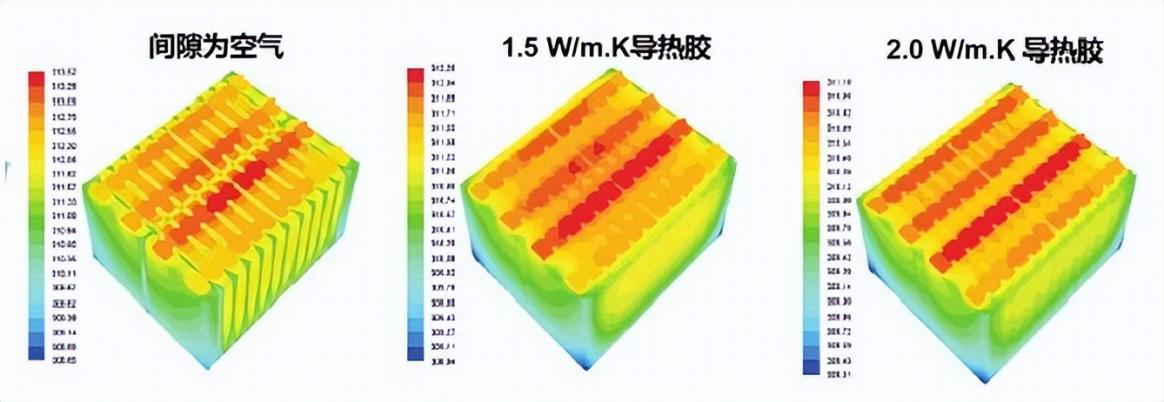
Different from the performance selection of thermal conductive adhesive in 5g communication base station (the maximum thermal conductivity is close to 10 W / m.k), the thermal conductive adhesive selected in the power battery industry not only needs to meet the requirements of thermal conductivity, but also needs to be comprehensively considered in terms of bonding performance, lightweight, low cost and even volatile. Therefore, the thermal conductivity is often maintained in the range of 1.2-2.0 w / M.K.
However, due to the limitation of material technology, the higher the thermal conductivity at this stage, the higher the density and cost of thermal conductive adhesive. Battery manufacturers cannot choose silicone products with high thermal conductivity (> 3.0 w / m.k) under the trend of large demand for thermal conductive adhesive and continuous cost reduction. At the same time, due to the continuous reduction of the design conditions of the structural parts of the battery pack, the thermal conductive adhesive needs not only the thermal conductive function, but also the bonding and fixing function with high strength (greater than 10 MPa). Therefore, the polyurethane thermal conductive structural adhesive with advantages of bonding strength and economic cost has become a realistic choice for many battery factories and new energy vehicle factories.
Ancham's solution
Ancham new material has launched a number of product series with thermal conductivity of 0.4-2.0 w / m.k and bonding strength of 6-15 MPa for power battery structure bonding and thermal conductivity structure bonding. It cooperates with customer partners to enable customers to participate in formula research and product development in the whole process, so as to meet the actual application requirements of customers.
At present, with the continuous promotion of the dual carbon plan, the new energy vehicle industry has ushered in a new outlet. With the influx of more and more consumers into the new energy vehicle market, the process level of new energy vehicles will be innovated. New requirements are also put forward for the sealant with multiple functions such as bonding, sealing, heat conduction and shockproof in new energy vehicles.